Extinguisher. I couldn’t find any locations for the FE that I found acceptable. So this is what I came up with. Obviously this is a very rough early design but this solution will absolutely work.. No it does not touch any of the control rods or tubes. It has a least a quarter of an inch clearance. It fits seamlessly and unobstructively underneath the passenger seat in its own storage tube.
I am only sharing this ugly mock up, to share the idea. Not to brag about my ugly craftsmanship, hahaha.
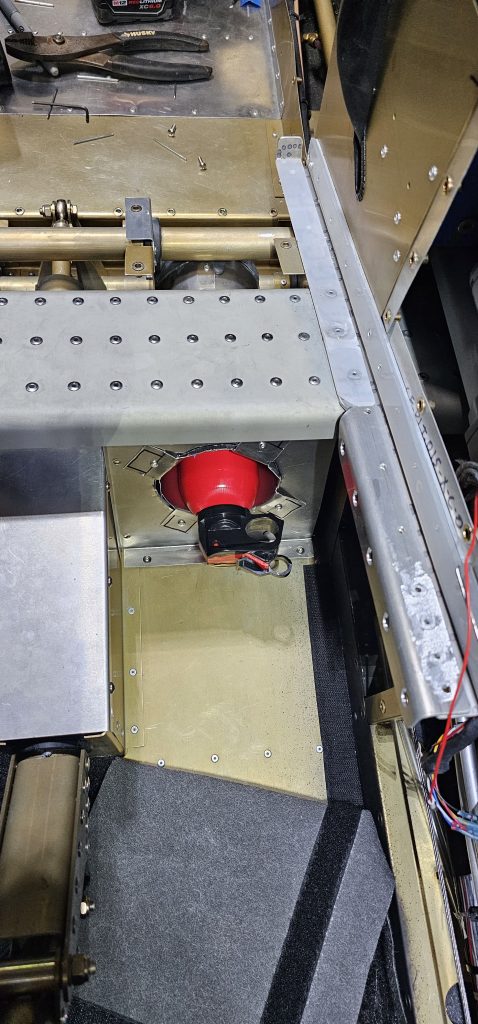

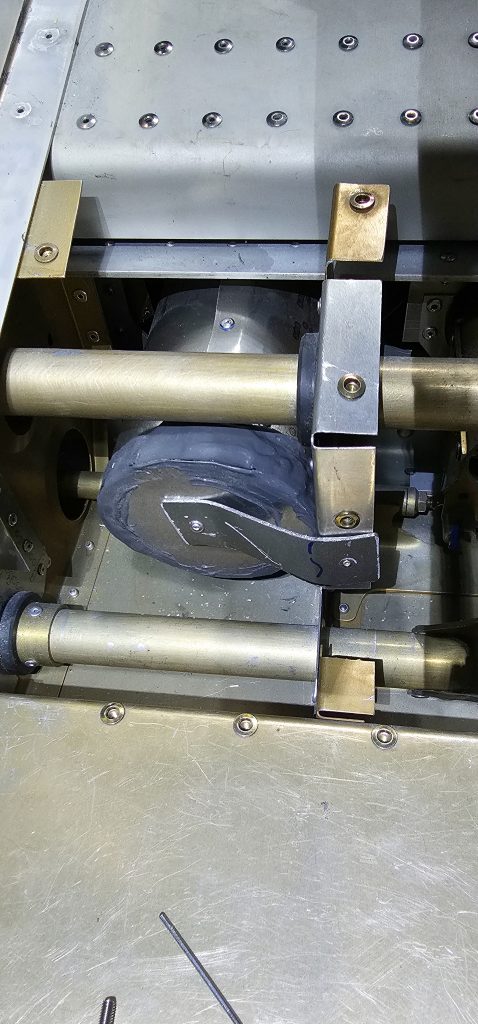